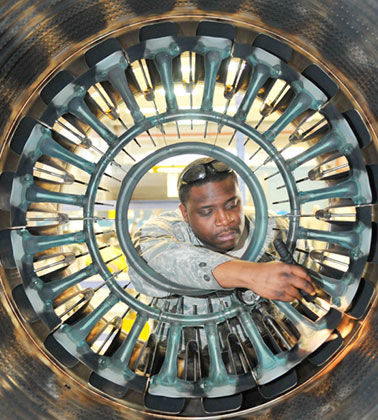
¿Cuándo debe usted, como operador, calificar su autoclave de laboratorio y validar un proceso? ¿Qué hay que tener en cuenta?
La necesidad de calificar un autoclave y de validar el proceso de esterilización se encuentra, en entre otros, en la Ley de Medicamentos, la Ley de Dispositivos Médicos, la Ley de Sustancias Químicas, y el Reglamento de Ingeniería Biotecnológica y Genética.
Estas leyes y reglamentos se refieren a veces a directivas, resoluciones o decisiones de la Comisión, directrices y normas.
De acuerdo con las directrices, las instalaciones y los procesos que participan directamente en el proceso de fabricación de grupos de productos como productos farmacéuticos, ingredientes activos, cosméticos, alimentos, piensos y productos médicos y que, por lo tanto, influyen en la calidad de los productos, se han de calificar y validar.
Los requisitos de las directrices de los principios de buenas prácticas de laboratorio se dirigen a los laboratorios que realizan estudios no clínicos sobre productos de ensayo como medicamentos, productos fitosanitarios, biocidas, productos cosméticos, medicamentos veterinarios, aditivos alimentarios, aditivos para piensos y productos químicos industriales. Esto incluye también las instalaciones y los procesos utilizados para inactivar los materiales de las muestras humanas (fluidos corporales, tejidos, cultivos celulares, etc.), microorganismos, cultivos celulares, endoparásitos, incluidas sus formas genéticamente modificadas.
Uno de los requisitos de los principios de las buenas prácticas de laboratorio es que los dispositivos, incluidos los sistemas informatizados validados, utilizados para recoger, registrar y reproducir datos y para controlar las condiciones ambientales pertinentes para el ensayo deben tener un diseño y un rendimiento adecuados. Si su autoclave está incluida de forma directa en los estudios de los grupos de productos antes mencionados, debe demostrar su idoneidad en términos de diseño y rendimiento.
Las autoridades de supervisión, los requisitos de calificación y aplicación de la validación, y la documentación se definirán más detalladamente mediante la especificación de normas, directrices, etc., o se basarán en normas, ya que la normalización también se mueve dentro de ciertos límites.
Calificación y Validación
Como operador de una autoclave que participa en su proceso de fabricación, o como operador de un laboratorio, usted es responsable de su proceso de producción o de los resultados y conclusiones de su estudio. La calificación y validación se llevan a cabo a menudo con la ayuda de un proveedor de servicios debidamente cualificado. Dado que solo usted puede definir los requisitos específicos del producto para su proceso, es necesaria una estrecha colaboración entre sus departamentos especializados, el calificador/validador y el fabricante de la autoclave. Incluso si los términos calificación y validación se mencionan habitualmente en una frase o incluso se utilizan como sinónimos, ocultan declaraciones y enfoques diferentes. Lo común de ambos términos es que se deben proporcionar documentos que cumplan las directrices y que contengan la definición de las pruebas individuales y la documentación de los resultados de las pruebas. En muchos casos, el plan por escrito de calificación/validación también incluye protocolos utilizados para documentar los resultados de las pruebas durante la ejecución.
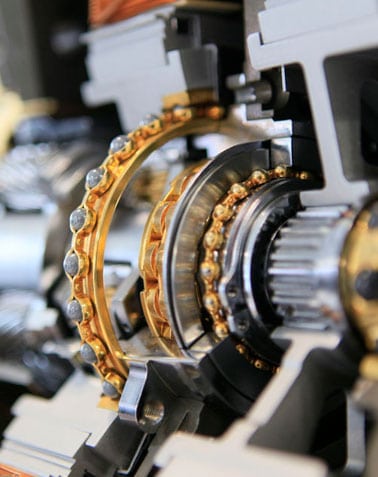
-
Calificación: En el marco de la calificación de las instalaciones, se debe demostrar que cuentan con la tecnología adecuada para la tarea prevista, que funcionan perfectamente y que ofrecen resultados que cumplen los requisitos. Por lo tanto, el objetivo principal es la instalación (la autoclave) y su propio funcionamiento correcto.
-
Validación: El objetivo de la validación de un proceso es demostrar que el proceso es eficaz y que entrega de forma reproducible un producto (resultado) que cumple los requisitos de calidad estipulados. Por lo tanto, la atención se centra principalmente en el proceso en sí y en la acreditación del cumplimiento de los criterios de aceptación que debe definir el operador de la instalación.
DQ: Calificación de diseño (Design Qualification)
La primera etapa de calificación de una autoclave comienza virtualmente en el momento en que usted formula y documenta sus requerimientos para el dispositivo a comprar. Con esto ya crea su User Requirement Specification (URS). Es decir, los requisitos que se imponen a un dispositivo y que deben cumplirse. Las autoclaves de muchos fabricantes pueden equiparse con opciones que influyen, por ejemplo, en la precisión o la velocidad del proceso. Si en la URS no se tienen en cuenta ciertas opciones en función de los procesos a realizar, y no se adecua el dispositivo en consecuencia, esto puede hacer mucho más difícil o incluso impedir la calificación y la validación con éxito. Ya en esta fase, los futuros operarios deberán especificar exactamente para qué se va a utilizar la autoclave, qué requisitos se van a aplicar a los procesos y qué normas y directrices se van a observar. Dependiendo de la complejidad de la instalación o de la autoclave, el alcance de la URS variará enormemente. Los proveedores de autoclaves presentarán una oferta sobre esta base y, en coordinación con el operador y el fabricante, se elaborarán especificaciones. El control de conformidad es un componente elemental del primer nivel de calificación: la calificación del diseño (DQ). Después de un DQ satisfactorio, el fabricante produce el dispositivo según las especificaciones acordadas. Ahora, la preparación de los documentos (plan de validación) necesarios para los pasos siguientes IQ, OQ y PQ puede iniciarse en paralelo (ya sea internamente, con el fabricante o con un proveedor de servicios independiente). Estos documentos constituyen la base para la aplicación de las IQ, OQ y PQ y especifican las revisiones y pruebas a realizar, así como sus parámetros y criterios de aceptación. Se requiere documentación detallada para demostrar que todos los controles y pruebas se han completado con éxito.
IQ: Calificación de instalación (Installation Qualification)
Después de completar con éxito la calificación de diseño y la entrega satisfactoria del dispositivo, puede comenzar el siguiente nivel de calificación de la autoclave en el sitio: la calificación de la instalación (IQ). Aquí, la idoneidad del lugar de instalación, las características físicas de la autoclave suministrada y el nivel de detalle de la documentación perteneciente al dispositivo se comprueban y documentan en los documentos de calificación. La documentación suele incluir instrucciones de funcionamiento, mantenimiento, limpieza y calibración, así como certificados de materiales y hojas de datos de los componentes individuales instalados. Si este nivel de calificación también se completa con éxito, o si se han evaluado las posibles desviaciones encontradas sobre la base de un análisis de riesgos y se han tomado las medidas correctivas adecuadas, se puede iniciar la calificación funcional (OQ) de la instalación.
OQ: Calificación funcional (Operational Qualification)
Con esta se acredita que los dispositivos, instalaciones, utilidades o sistemas cumplen con los requisitos y especificaciones del operador, los cuales se definieron en el marco de la calificación de diseño. Se realizan pruebas para comprobar que el dispositivo funciona según lo previsto. Esto incluye la calibración, así como la simulación de las condiciones de error, fallo y desconexión del dispositivo. Este procedimiento sirve como prueba documentada de que los defectos que puedan ser relevantes para la seguridad o afectar la calidad del producto se detectan correctamente por la autoclave. La realización de las series de esterilización de la autoclave sin producto introducido también forma parte del ámbito de la calificación funcional. Aquí se introducen sensores de temperatura y un sensor de presión en la autoclave, los cuales miden la presión y la temperatura por medio de un registrador de datos independientemente del control de la autoclave. Los valores de temperatura y presión determinados de esta manera se pueden comparar con los valores determinados por el sistema de control de la autoclave. Además, se introducirán en las autoclaves bioindicadores basados en Bacillus Stearothermophilus para comprobar la eficacia biológica del proceso de esterilización. El objetivo es la prueba documentada de que una instalación o un dispositivo, sin producto, es adecuado para el uso previsto.
PQ: Calificación de rendimiento (Performance Qualification)
Una vez que se ha comprobado que la autoclave funciona correctamente sin producto, se comprueba el rendimiento del dispositivo de acuerdo con las especificaciones del plan de validación previamente definido, con el objetivo de demostrar que los requisitos de proceso definidos se cumplen adecuadamente en condiciones reales (con producto). Hay que tener en cuenta que la distribución de la temperatura depende del producto a esterilizar y, por lo tanto, se debe realizar una prueba de PQ por separado para cada configuración de carga. Para ello, se definen patrones de carga que deberían ser representativos de las cargas que se esperan en el funcionamiento diario. Esto se hace a menudo de acuerdo con el siguiente esquema: – Carga mínima – Carga media – Carga en el peor de los casos.
En cualquier caso, sin embargo, la carga en el peor de los casos debe verificarse en relación con, por ejemplo, la cantidad de carga. Puede ser necesario considerar otros parámetros si pudieran influir en el resultado del proceso de esterilización. Al igual que en el OQ, el proceso de esterilización es controlado por sensores de temperatura y presión que registran los datos correspondientes por medio de un registrador de datos, de forma independiente al sistema de control de la autoclave. Además, la efectividad biológica del proceso de esterilización también se comprueba mediante los indicadores de referencia basados en Bacillus Stearothermophilus. A diferencia del OQ, en el PQ los sensores de temperatura y también los bioindicadores se colocan en el producto a probar (muestra de carga) con el fin de demostrar la eficacia esterilizante del producto. Es importante que los sensores de temperatura y también los bioindicadores se coloquen en las zonas del producto en las que es de esperar que el efecto de esterilización sea más difícil de conseguir. El objetivo es la prueba documentada de que el proceso en consideración proporciona de forma reproducible el resultado esperado. Al realizar la OQ y la PQ, el número de puntos de medición de temperatura dentro del espacio utilizable debe cumplir con las recomendaciones de las normas pertinentes, como la EN 556 o las directrices GxP, ya que cualquier desviación de estas normas probablemente dará lugar a preguntas durante una inspección. Así, se deben proporcionar 12 puntos de medición de temperatura por cada m3 de sala de esterilización. En cada punto de medición de la temperatura se coloca un bioindicador basado en Bacillus Stearothermophilus.
Revalidación
Si todos los niveles de cualificación y la validación (o validaciones) del proceso se han completado con éxito, el operador debe definir un intervalo para la revalidación. Aquí tiene sentido ponerse de acuerdo con el fabricante de la autoclave, ya que es apropiado combinar la revalidación con la necesaria calibración recurrente de los sensores del dispositivo. Se requiere precaución al cambiar los parámetros del proceso. Esto incluye, por ejemplo:
- Cambios en los parámetros del dispositivo (por ejemplo, cambio de temperatura o tiempo de esterilización)
- Cambios en la configuración de carga o en la composición del producto a esterilizar
- Modificación de embalajes de los productos embalados
- Reparaciones en dispositivos y sustitución de componentes asociados
- Actualizaciones del software del dispositivo
Si se producen los cambios mencionados anteriormente, se debe examinar su influencia en el proceso global validado. Si es de esperar que el cambio pueda tener impacto en el proceso global, la influencia debe determinarse, evaluarse y documentarse como parte de una revalidación. Si es necesario, esto puede dar lugar a los ajustes necesarios en el proceso global para que pueda seguir cumpliendo con los parámetros definidos antes de la modificación. Dado que los cambios pueden ser lentos o parciales, es decir, difíciles o incluso imperceptibles, la revalidación debe realizarse siempre a intervalos fijos. Aquí los intervalos anuales han demostrado su validez. Para procesos particularmente críticos, el intervalo para la revalidación también puede especificarse a intervalos más cortos.
Las autoclaves se pueden configurar de modo que permitan una validación del proceso de esterilización y lograr así que la esterilización en laboratorios de seguridad, salas limpias y espacios de producción sea reproducible y demostrable. Estaremos encantados de ayudarle en la cualificación y validación de sus procesos de esterilización.
- Cualificación del diseño (DQ)
- Cualificación de la instalación (IQ)
- Cualificación operativa (OQ)
- Cualificación de procesos (PQ)
Todas las etapas del proceso de cualificación pueden realizarse a través de personal cualificado y documentarse según los requisitos GMP.
Los autoclaves también se pueden utilizar para otras aplicaciones, tales como pruebas de esfuerzo (tests de materiales) y para simular procesos industriales de esterilización.
Cuéntenos sus necesidades para que podamos crear junto a usted una autoclave perfecta en cuanto a tamaño y tecnología para sus necesidades. Confíe en nuestros más de 20 años de experiencia en el campo de las autoclaves, esterilizadores de vapor y en el desarrollo de métodos incluso para los procesos de esterilización más complejos.